1. What is casting.
Usually refers to the method of making products from molten alloy materials, injecting liquid alloys into pre-made casts, cooling, solidifying, and obtaining blanks and parts of the required shape and weight.
2. Metal mold casting.
Metal casting, also known as hard casting, is a casting method in which liquid metal is poured into metal casting to obtain casting. Casting molds are made of metal and can be reused many times (hundreds to thousands of times). Metal mold casting can now produce castings that are limited in weight and shape. For example, ferrous metals can only be castings with simple shapes, the weight of the castings cannot be too large, and the wall thickness is also limited, and the wall thickness of small castings cannot be cast.
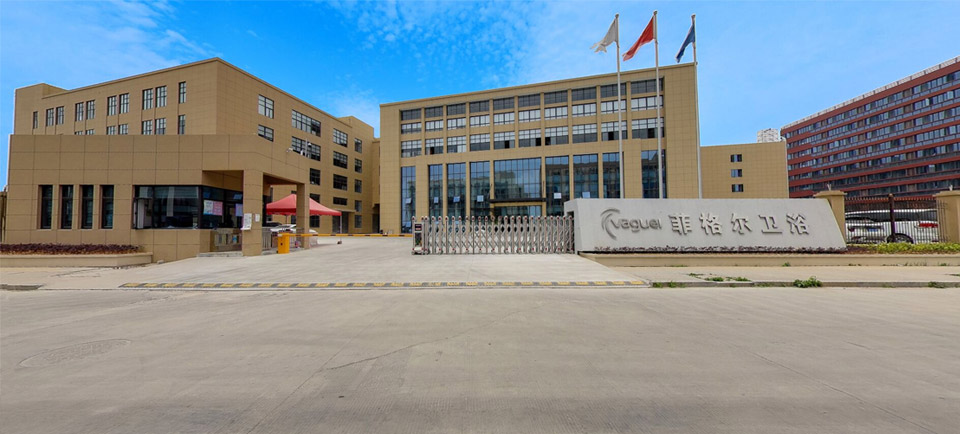
3. Sand casting.
Sand casting is a traditional casting technology that uses sand as the main molding material. The molding materials used in sand casting are cheap, simple to cast, and can be adapted to single-piece production, mass production and mass production of castings. It has long been the basic technology of casting production.
4. Gravity casting.
Refers to the technology of casting molten metal (copper alloy) under the gravity of the earth, also known as metal casting. It is a modern process of making hollow casting molds with heat-resistant alloy steel.
5. Cast copper alloy.
The raw material used for faucet products is cast copper alloy, which has good casting properties, mechanical properties, corrosion resistance, and the castings have fine organization and compact structure. The alloy grade is ZCuZn40P62 (ZHPb59-1) according to GB/T1176-1987 casting copper alloy process conditions, and the copper content is (58.0~63.0)%, which is the most ideal leading casting material.
6. Brief description of the faucet casting process.
First of all, on the automatic hot core box core shooting machine, the sand core is produced for standby, and the copper alloy is smelted (resistance furnace of the smelting equipment). After confirming that the chemical composition of the copper alloy meets the requirements, pour it (the pouring equipment is a metal mold gravity casting machine). After cooling and solidification, open the mold discharge and clean the outlet. After all the copper water in the resistance furnace is poured, self-check the cooled casting. Send it to the shakeout drum for cleaning. The next step is the heat treatment of the casting (stress removal annealing), the purpose is to eliminate the internal stress generated by the casting. Put the billet into the shot blasting machine for a more ideal casting billet, and ensure that the inner cavity is not attached with molding sand, metal chips or other impurities. The casting billet was fully enclosed, and the air-tightness of the box and the air-tightness of the partition were tested in water. Finally, the classification and storage are checked through quality inspection analysis.
Post time: Feb-09-2022